Custom Monoblock Solution for Hygienic Food Packaging
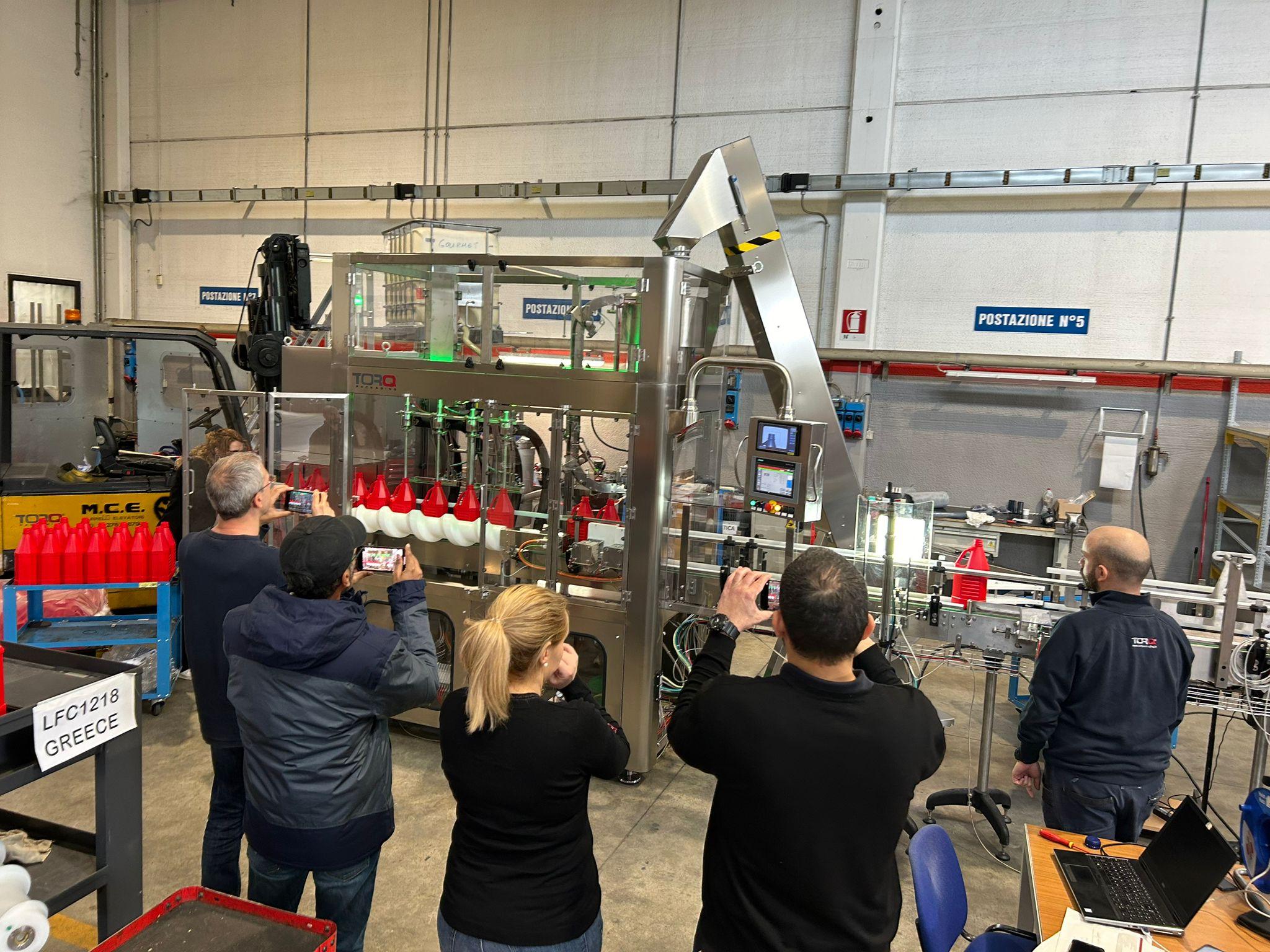
We recently delivered a fully automated monoblock system designed for a leading food producer to meet their stringent hygiene, flexibility, and filling accuracy requirements. The machine integrated both filling and capping processes into one compact unit, helping the client ensure product safety and streamline their operations.
Client Requirements:
The client required a monoblock solution capable of:
- Hygienic design to handle liquid food products like ketchup, ensuring compliance with food safety standards.
- Flexible operations to accommodate multiple bottle sizes and ensure quick changeovers between product formats.
- High filling accuracy for viscous, hot-filled products at controlled temperatures.
- A fully electronically controlled system to minimize operator intervention and ensure precision throughout the production process.
Our Solution:
To meet these requirements, we developed a highly adaptable and hygienic monoblock filler-capper system:
- Hygienic Design: The machine’s construction followed strict food safety guidelines, featuring stainless steel materials for all parts in contact with the product. The fully automated Cleaning in Place (CIP) system ensured a hygienic production process by cleaning the filler nozzles, tank, and wetted parts at 85°C, with minimal manual involvement.
- Filling Accuracy: The monoblock system was designed to fill bottles within exact net weight specifications, ensuring product consistency and reducing wastage. The machine handled viscous liquids, such as hot-filled ketchup at 70°C, with high precision, adapting to the product's specific viscosity.
- Flexibility: The system could handle various bottle formats, including 3L and 5L jerrycans, with quick and tool-free changeovers between different sizes in less than 10 minutes. This flexibility allowed the client to run multiple product lines without significant downtime, enhancing overall production versatility.
- Fully Electronic Control: The machine was equipped with advanced electronic controls to automate every aspect of the process, from bottle infeed to precise filling and capping. Sensors and control systems ensured smooth operation, identifying and correcting bottle orientation and other variables without human intervention. The electronic interface also allowed for remote monitoring and diagnostics, enhancing overall process control.
The hygienic design of the monoblock system ensured that the client met all required food safety standards while achieving accurate and consistent filling. The flexibility of the system allowed for easy changeovers between bottle formats, providing the client with a versatile solution capable of adapting to different production needs. Additionally, the fully electronic control system minimized operator input, reducing the risk of errors and ensuring a reliable, automated process.
Conclusion:
This project highlighted our ability to deliver customized, hygienic solutions that prioritize flexibility and accuracy. The integration of a monoblock filler-capper into the client's production line improved both operational efficiency and product quality, while the hygienic design and fully electronic controls ensured a safe and reliable manufacturing process.