Soluzione Monoblocco Personalizzata per il Confezionamento Alimentare Igienico
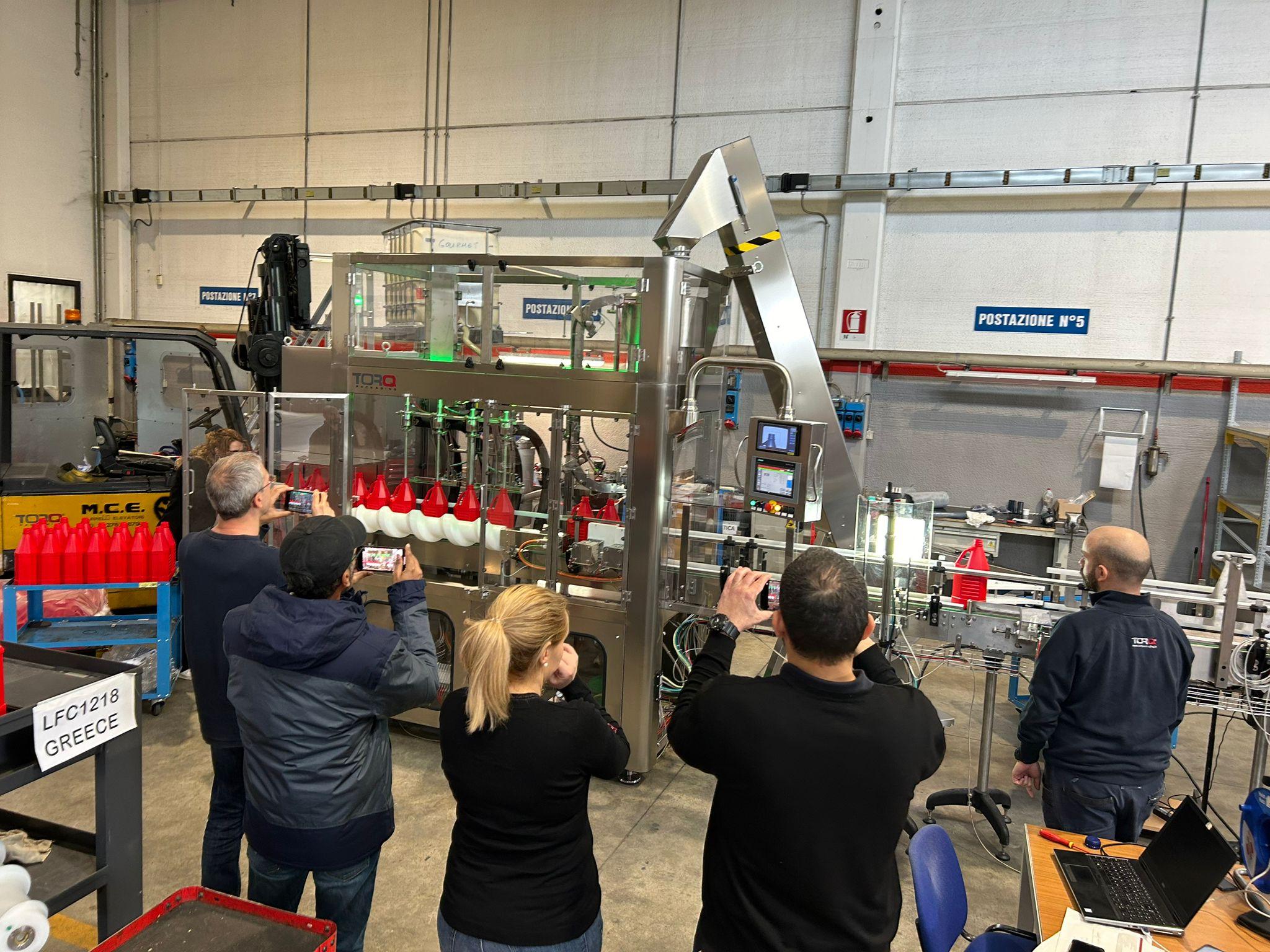
Abbiamo recentemente consegnato un sistema monoblocco completamente automatizzato progettato per un importante produttore alimentare, al fine di soddisfare i loro rigorosi requisiti di igiene, flessibilità e precisione nel riempimento. La macchina integra i processi di riempimento e tappatura in un'unica unità compatta, permettendo al cliente di garantire la sicurezza del prodotto e ottimizzare le operazioni.
Esigenze del Cliente:
Il cliente richiedeva una soluzione monoblocco in grado di:
- Garantire un design igienico per la gestione di prodotti alimentari liquidi come il ketchup, rispettando gli standard di sicurezza alimentare.
- Offrire operazioni flessibili per adattarsi a diversi formati di bottiglie e garantire cambi rapidi tra i formati dei prodotti.
- Assicurare un’alta precisione di riempimento per prodotti viscosi riempiti a caldo, con controllo della temperatura.
- Integrare un sistema completamente elettronico per minimizzare l'intervento dell'operatore e garantire precisione durante tutto il processo di produzione.
La Nostra Soluzione:
Per soddisfare queste esigenze, abbiamo sviluppato un sistema monoblocco filler-tappatore altamente adattabile e igienico:
- Design Igienico: La costruzione della macchina ha seguito rigorose linee guida per la sicurezza alimentare, con materiali in acciaio inossidabile per tutte le parti a contatto con il prodotto. Il sistema completamente automatizzato di Cleaning in Place (CIP) ha garantito un processo produttivo igienico, pulendo gli ugelli di riempimento, il serbatoio e le parti bagnate a 85°C, con un intervento manuale minimo.
- Precisione di Riempimento: Il sistema monoblocco è stato progettato per riempire le bottiglie rispettando esattamente le specifiche del peso netto, garantendo coerenza nel prodotto e riducendo gli sprechi. La macchina ha gestito liquidi viscosi, come il ketchup riempito a caldo a 70°C, con alta precisione, adattandosi alla viscosità specifica del prodotto.
- Flessibilità: Il sistema è in grado di gestire diversi formati di bottiglie, inclusi taniche da 3L e 5L, con cambi rapidi e senza utensili tra i vari formati in meno di 10 minuti. Questa flessibilità ha permesso al cliente di gestire più linee di prodotto senza tempi morti significativi, migliorando la versatilità complessiva della produzione.
- Controllo Completamente Elettronico: La macchina è dotata di avanzati controlli elettronici per automatizzare ogni aspetto del processo, dall’alimentazione delle bottiglie al riempimento e tappatura precisi. Sensori e sistemi di controllo hanno garantito un funzionamento fluido, identificando e correggendo l'orientamento delle bottiglie e altre variabili senza l'intervento umano. L'interfaccia elettronica ha inoltre consentito il monitoraggio e la diagnostica remota, migliorando il controllo generale del processo.
Il design igienico del sistema monoblocco ha garantito al cliente il rispetto di tutti gli standard di sicurezza alimentare richiesti, garantendo al contempo un riempimento accurato e coerente. La flessibilità del sistema ha permesso cambi rapidi tra i formati delle bottiglie, fornendo al cliente una soluzione versatile in grado di adattarsi alle diverse esigenze di produzione. Inoltre, il sistema di controllo completamente elettronico ha ridotto al minimo l'intervento dell'operatore, riducendo il rischio di errori e garantendo un processo automatizzato affidabile.
Conclusione:
Questo progetto ha evidenziato la nostra capacità di fornire soluzioni personalizzate e igieniche che danno priorità alla flessibilità e alla precisione. L'integrazione di un monoblocco filler-tappatore nella linea di produzione del cliente ha migliorato sia l'efficienza operativa sia la qualità del prodotto, mentre il design igienico e i controlli completamente elettronici hanno assicurato un processo di produzione sicuro e affidabile.