Trigger Capping Machine
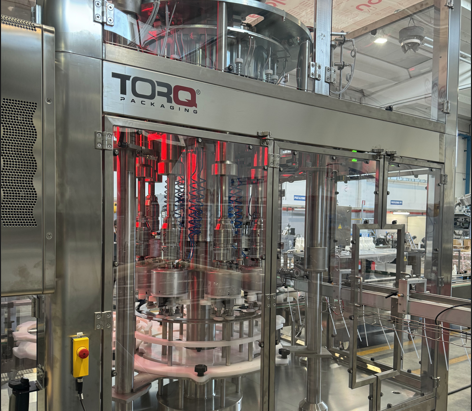
Client: A leading multinational consumer goods company managing a portfolio of over 400 brands across various sectors including food, beverages, hygiene products, and home care items.
- Project: Home Care Liquids
- Machine: Trigger Capper Applicator & Sorter
- Location: Confidential
- Operational Speed: 150 bottles per minute (bpm)
Introduction
A renowned multinational consumer goods company commissioned an innovative Trigger Capping Machine to enhance their packaging capabilities for liquid home care products. This machine was carefully designed and built to meet the producer's high standards for efficiency, reliability, and quality.
Project Requirements
The machine's primary function is to cap triggers on bottles filled at the filling station, ensuring that the triggers are correctly oriented and securely attached. Key requirements included:
- Efficiency: The machine must operate at an efficiency of not less than 98%.
- Quality Control: Automated detection and rejection of defective triggers and bottles.
- Flexibility: Ability to handle various types and sizes of triggers and bottles, including both snap-on and screw-on types.
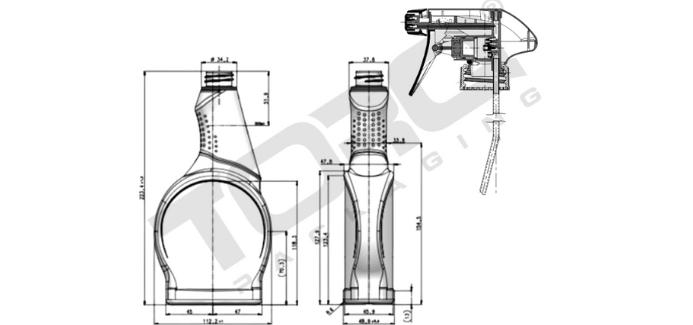
Machine Features
The Trigger Capping Machine includes several advanced features. The In-feed Trigger Supply System ensures a continuous and controlled supply of triggers to the capping station.
The Bottle Handling System transports bottles in an upright position from the filling station to the capping station without causing spillage.
The Trigger Orientation and Sorting feature automatically orients and sorts triggers to ensure correct placement on bottles.
The Reject System includes an Integrated Vision Reject System to control capping quality, integrated with a multi-push reject system on a motorized lateral conveyor. This multi-push system works like hands with fingers to gently move the bottles, avoiding spillage and ensuring that open bottles do not proceed down the line.
Finally, the Discharge System ensures correctly capped bottles are fed onto the discharge conveyor for further processing.
The Trigger Capping Machine project successfully met the large-scale producer's stringent requirements, providing a reliable and efficient solution for their packaging needs. The machine's design and build process emphasized quality, safety, and operational efficiency, ensuring it would serve the production line effectively.
The producer can achieve higher productivity and maintain their commitment to quality in their home care products with this mechanical capping solution. The machine's ability to operate at 150 bottles per minute is a testament to its advanced design and superior performance.
We look forward to discussing how we can help with your next project. Get in touch with us to explore how our solutions can meet your needs and drive your success.