Custom Packaging Line for Personal Care Products
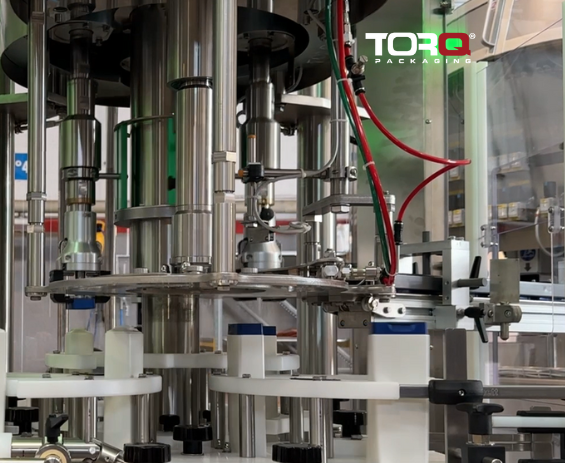
Client Overview
The client, a major player in the personal care industry, needed a highly flexible packaging line capable of handling a diverse range of bottle sizes and cap formats. The goal was to improve production efficiency while maintaining high standards of quality and precision across various personal care product types.
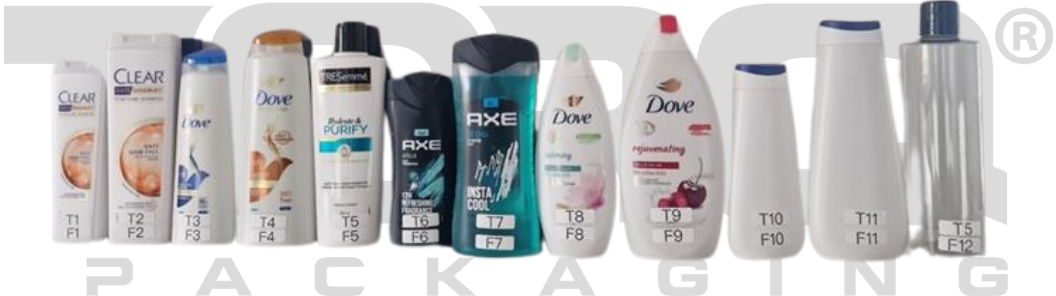
Project Requirements
The project involved developing a complete packaging line that could handle multiple bottle and cap combinations. Key requirements included:
- Components: The line was composed of a bottle unscrambler, linear filler, rotary capper, and rotary labeller.
- Speed and Output: The line needed to operate at 100 bottles per minute (bpm) for 400ml bottles, which translates to 6000 bottles per hour.
- Bottle and Cap Flexibility: The line was designed to work with a wide range of bottle formats (12 distinct sizes) and cap styles (11 different variations). This flexibility was crucial to accommodate different product types, ranging from small to large containers, and various cap mechanisms, such as oriented flip-top and screw caps.
Technical Approach
- Bottle Sorting and Feeding: A sophisticated bottle unscrambler was installed to manage different bottle shapes and sizes. The unscrambler efficiently feeds the bottles into the production line, ensuring minimal handling and optimal positioning for filling.
- Filling Station: The linear filler was designed with precision to avoid foaming risks while handling various viscosities. It is equipped with 12 filling valves, ensuring accuracy in filling different bottle formats while maintaining hygiene standards. The system is fully adaptable to the product’s characteristics, such as density and temperature.
- Capping System: The rotary capper was developed to handle multiple cap styles, ensuring consistent torque application for both flip-top and screw caps. The system’s design allows for quick and easy changeovers, minimizing downtime during format changes.
- Labelling: The rotary labeller efficiently applies labels to both cylindrical and uniquely shaped bottles. The flexibility of the system allows for the seamless application of front and back labels, ensuring product traceability and brand consistency (client-specific details).
Customization and Development
The project required a highly customized solution to meet the client’s diverse production needs. The bottle and cap handling systems were designed to offer quick changeover capabilities, allowing the production line to switch between different formats in minimal time. This adaptability was critical, as the client needed to produce various product types within the same production cycle.
Challenges and Solutions
The wide range of bottle and cap formats presented significant challenges in ensuring smooth transitions and handling across the line. To address these, the team implemented advanced timing screws and conveyor guides to maintain bottle stability during high-speed operations. Additionally, the capping system was fitted with an automated cap sorting mechanism that adapted to various cap formats, ensuring precise application without manual intervention.
Outcome
The custom-designed packaging line was successfully implemented, meeting all production speed, flexibility, and operational efficiency goals. By allowing quick format changes, the line helped the client optimize production time and reduce costs associated with downtime and format adjustments. The enhanced flexibility enabled the client to produce a variety of personal care products efficiently on the same line, ensuring high throughput and consistent product quality.
Let's Discuss Your Project
At Torq Packaging, we specialize in creating customized solutions tailored to your specific production needs. Whether you're looking to enhance efficiency, handle multiple product formats, or implement cutting-edge technology, we’re here to help. Contact us today to discuss your project and how we can work together to meet your goals.